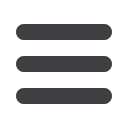
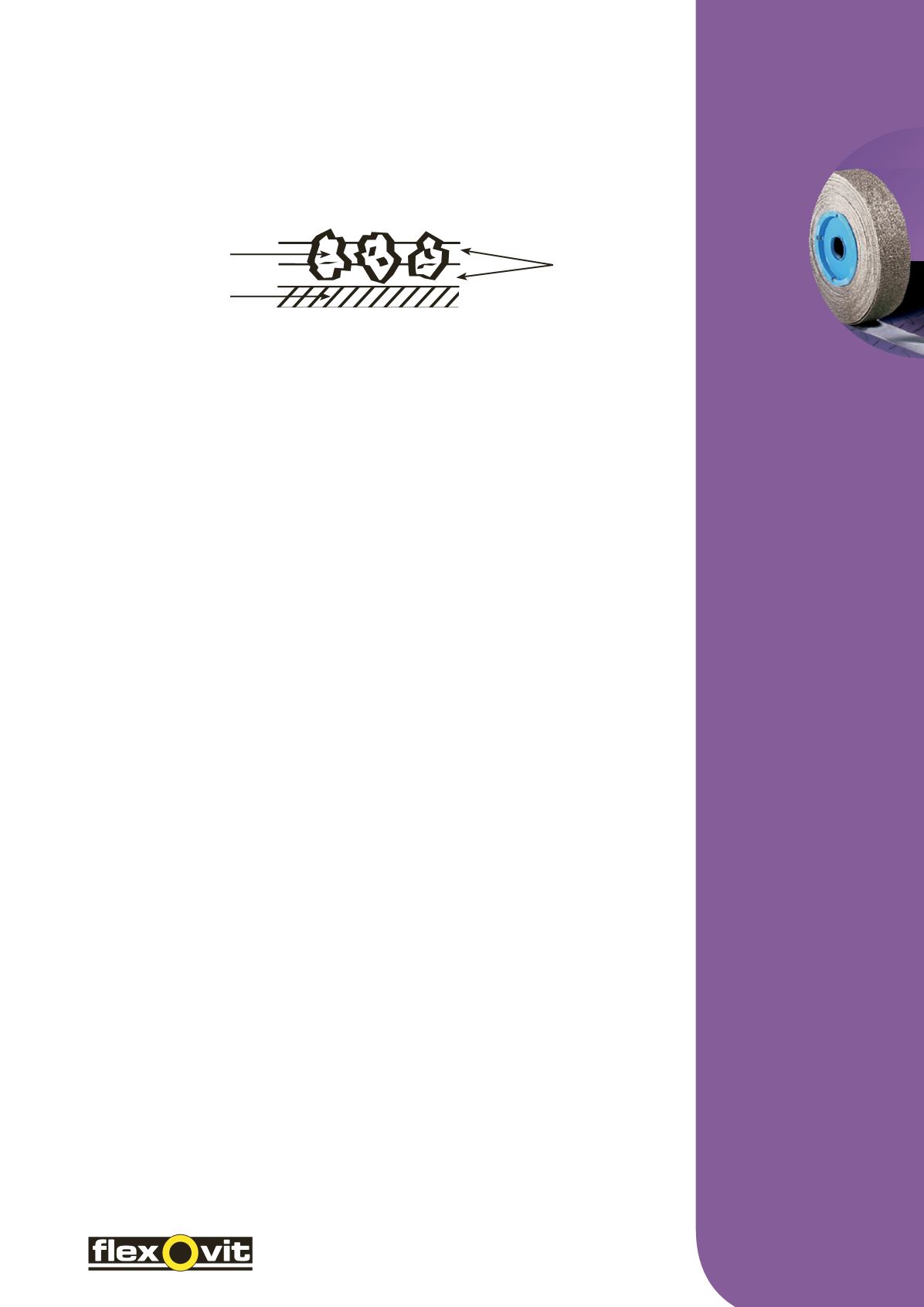
COATED
ABRASIVES
61
WHAT IS A COATED ABRASIVE?
Modern coated abrasives are the product of an extremely technical process developed through many years of
research and development. They remain, however, a product composed of three basic elements: a flexible or
semi-rigid backing to which abrasive grains are bonded by an adhesive.
ABRASIVES TYPES
ABRASIVES
The ideal abrasive grain offers maximum resistance to point wear, yet fractures before serious dulling occurs,
thereby satisfying both stock removal and finishing requirements.
Aluminium Oxide
is tough and well adapted to grinding high tensile materials, such as carbon steel, alloy
steels, tough bronze and hard woods. Wherever toughness (ability to resist fracturing) is the main consideration,
aluminium oxide outperforms all other coated abrasive grains.
Zirconia Alumina
has a unique self-sharpening characteristic which gives it long life on rugged stock removal
operations. Zirconia alumina is well suited for heavy grinding of metals and planing of wood, because
the controlled fracturing of the grain continuously produces sharp, new abrading points.
Silicon Carbide
is the hardest and sharpest of the minerals used in coated abrasives. Its hardness
and sharpness make it the ideal abrasive for sanding non-ferrous metals (aluminium, brass, bronze, magnesium,
titanium, etc.), rubber, glass, plastics, fibrous woods, enamel and other relatively soft materials. Silicon carbide
is superior to any other abrasive in its ability to penetrate and cut faster under light pressure.
Ceramic Aluminium Oxide
is a long-lasting, tough, dense abrasive due to its micro structure.
The extremely small micron size particles break off during grinding, producing multiple new cutting edges.
As it stays sharp, especially when used in medium and high pressure operations, it cuts at a higher rate than
other abrasives. Recommended for use on forged and carbon steels, high nickel and cobalt alloys.
ABRASIVE GRAIN DISTRIBUTION
There are two types of abrasive grain coverage on the backing:
• Openly spaced distribution where between 30% and 60% of the backing is covered leaving
large spaces between each abrasive grain. It is used in operations where the grinding swarf would otherwise
‘load’ or clog the surface, reducing cutting efficiency and shortening the coated abrasive life
• Closely packed grain distribution is where the grain completely covers the backing. The greater number
of abrading points in a given area leads to faster stock removal. It is recommended where loading is not
a problem and where smoother surface finishes are desired
Bonds
Sizer coat
Maker coat
Abrasives
Backing