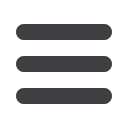
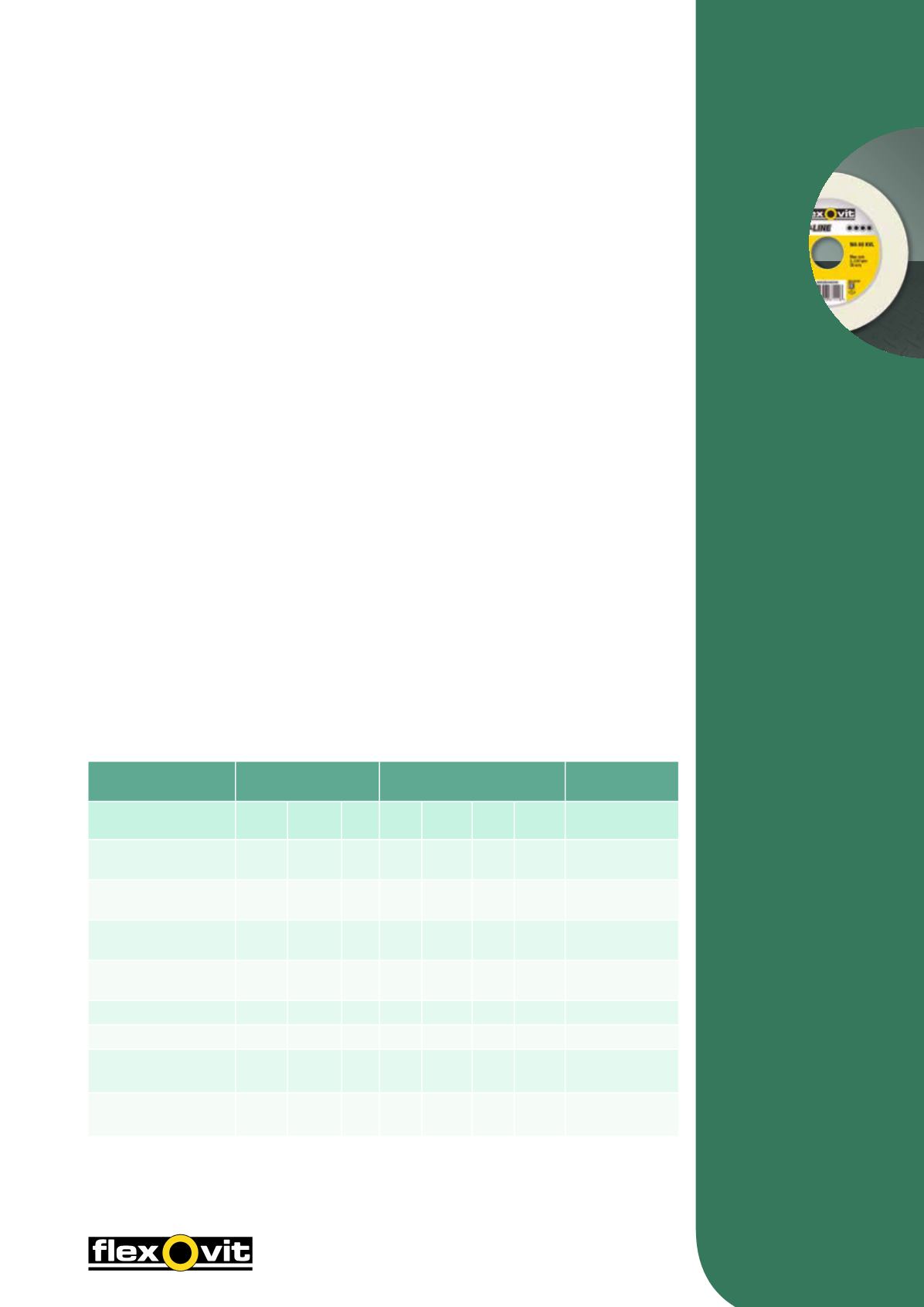
BONDED
ABRASIVES
229
Abrasive Type Size of the Abrasive
Grain
Hardness of the Bond Type of Bond
Coarse Medium Fine Soft
Med Hard
Extra
hard
WA = Alumunium
Oxide
C
M F Soft Med Hard VHard
V = Vitrified
73A = Ceramic
Abrasive
12
46 150 E
J
N S
B = Resinoid
48A = Semi-friable
Aluminium Oxide
14
54 180 F
K O T
BF = Resinoid
reinforced
A = Aluminium
Oxide
16
60 220 G L
P
U
E = Shellac
GC = Silicon Carbide
20
80 240 H M Q V
R = Rubber
C = Silicon Carbide
24 100 280 I
R W
41A = Aluminium
Oxide
30 120
X
44A = Aluminium
Oxide
36
WHAT IS A GRINDING WHEEL?
A grinding wheel is a precision tool with thousands of cutting points. It consists of abrasive grains held in a matrix
of bond and separated by pores. The abrasive grains are the cutting points while the purpose of the bond is to
hold the individual grains together. The pores (hollow spaces between adjacent abrasive grains and the bond)
serve to provide clearance for coolant penetration and metal chips removed in the grinding process.
When the wheel is rotated at grinding speed and applied to the workpiece, the abrasive grains cut the material
that is being ground, removing the material in small chips.
Under the action of the forces imposed during grinding the abrasive cutting points are worn flat, resulting in
the points becoming blunt. This causes an increase in friction, heat build up and the forces imposed on the wheel.
The increase in grinding forces causes either the abrasive to fracture, exposing new cutting edges, or fractures
the bond bridges holding the abrasive grains. In the latter case fresh abrasive grains are exposed to cut
the workpiece.
In normal vitrified grinding applications the wheel has to be dressed.
By varying the properties of the abrasive, the type of bond, the make-up of the wheel, it is possible to produce
grinding wheels with a vast range of different grinding characteristics.
ABRASIVES
Modern synthetic abrasives allow accurate control over the physical properties and form of the abrasive grain.
This helps to ensure that grinding wheels can be manufactured with consistent cutting properties.
Flexovit offers a comprehensive selection of abrasive types to provide a wide range of specific grinding
characteristics. This is necessary for maximum efficiency in the large variety of operations demanded by
the industry today.
Abrasive Grain Size
The grain or grit size is most important in determining a wheel’s ability to achieve the required surface finish
and remove stock. The size is designated by a number which increases as grain size decreases. For example
10 grit has a median size of about 2,0mm and 60 grit 0,25mm.
Standard sizes are used in all Flexovit wheels as specified in the European Standards laid down by FEPA.
An ideal grinding abrasive has the ability to stay sharp with minimum point dulling, and when dulling begins
it fractures revealing new sharp cutting edges. Abrasive grains used in the manufacture of bonded abrasives
come in three main categories: