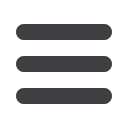
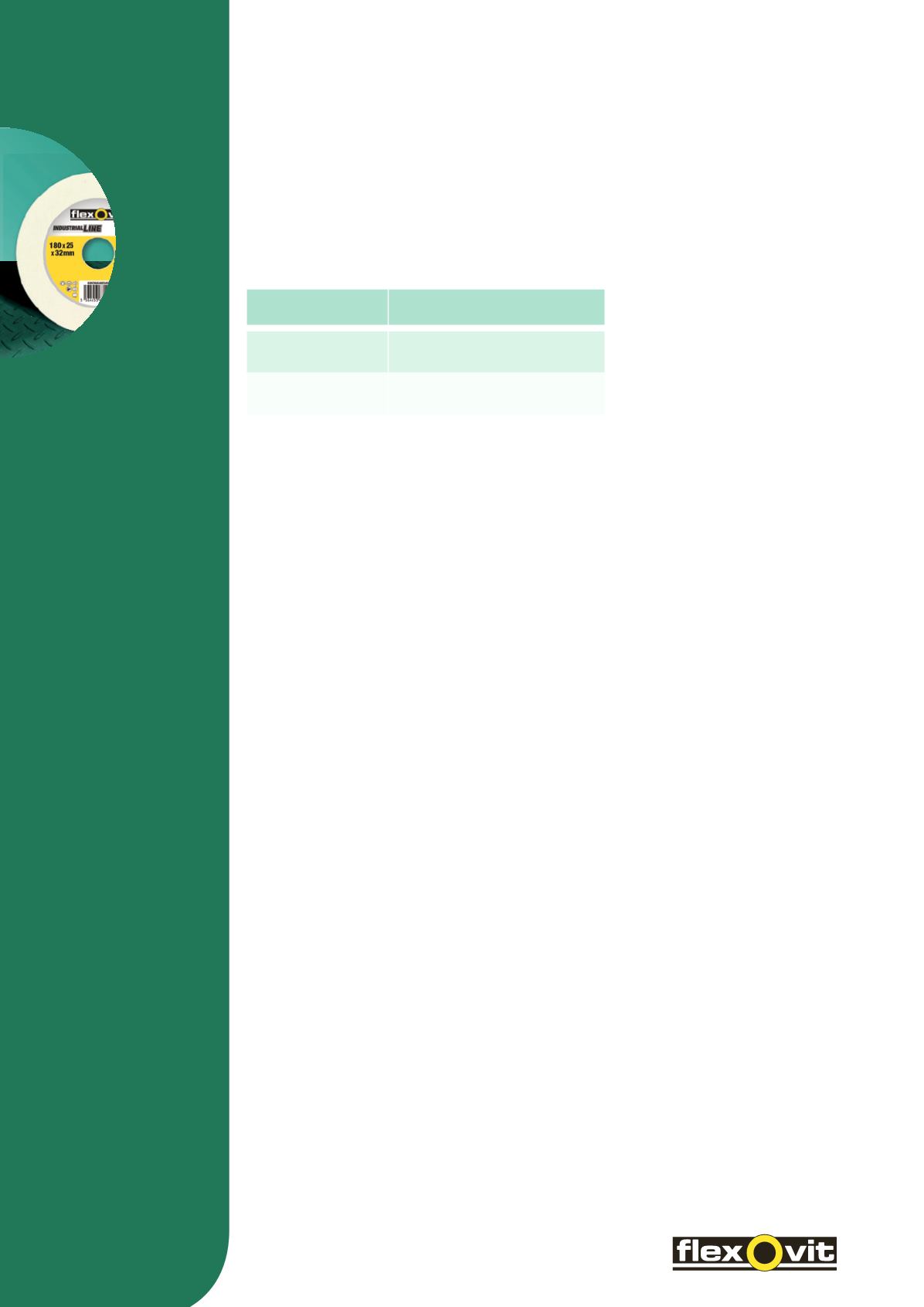
BONDED
ABRASIVES
230
TECHNICAL INFORMATION
Resinoid Bond
A number of different organic polymers are used to bond abrasives but generally resinoid bonds are based on
thermosetting phenolic resin. Resin bonds are cured by heating in ovens under carefully controlled conditions
at selected temperatures between 150°C and 200°C.
Resinoid wheels are tougher and less brittle than vitrified wheels. Their inherent toughness makes them ideally
suited to heavy duty operations or high operating speeds, often with the aid of fabric or steel ring reinforcement.
GRADE
Grade is a measure of the bonding strength of the wheel, usually referred to as ‘hardness’. Hardness will vary
according to the amount of bond and abrasive in the wheel. Grade is not a measure of the hardness
of the abrasive material but of the tenacity of the bond to hold the abrasive grains together.
Very hard abrasive can, theoretically, be bonded into a very ‘soft’ free cutting, fast wearing wheel, but an increase
in the amount of bond will make the wheel act harder.
The grade of all Flexovit wheels are designated by letters of the alphabet and can range from ‘E’ for very soft to ‘Z’
for the hardest. A + sign after the letter indicates a hardness slightly greater than the grade.
SELECTING THE RIGHT PRODUCT
There are nine main factors to be considered when selecting a grinding wheel for any application:
• The material to be ground – its type and hardness
• The stock to be removed
• The workpiece geometry and surface finishes required
• The grinding machine, the type of machine, the power available and its conditions
• Wheel speeds and feeds
• Grinding contact area
• Grinding fluid – whether the operation is wet or dry
• The severity of the grinding operation
• The dressing method
MATERIAL TO BE GROUND
The type of material affects the selection of abrasive, grit size and grade. Alumina type abrasives are the most
suitable for grinding high tensile materials such as steel and ferritic cast irons. The more friable types of alumina
are preferred on harder steels and applications having large arcs of contact.
Low tensile strength materials and non-metallic materials are most efficiently ground or cut with silicon carbide
abrasive.
The hardness of the material governs the amount of penetration that can be achieved by the abrasive. For this
reason finer grit size wheels are required to grind hard materials and soft materials are best ground with medium
to coarse grit size wheels.
For most efficient operation the grade must be adjusted to suit the hardness of the material. As a general guide,
the harder the material, the softer the grade of wheel required.
Grain
Bond
Aluminum Oxide
VL
VM
Low Temp
High Temp
Silicon Carbide
VK
VKP
Low Temp
High Temp
BOND
Flexovit supplies bonded abrasive products made using both resinoid and vitrified bonds.
Vitrified Bond
Vitrified bonded wheels have a porous structure composed of abrasive particles held together by bond bridges of glass
or similar vitreous material. Their strength is developed by firing in kilns at temperatures between 900°C to 1250°C.
Since vitrified bonded wheels are manufactured at such high temperatures, they are not affected by heat generated
during the normal grinding process. Individual bond bridges can, therefore, only be fractured by mechanical forces
imposed during grinding.