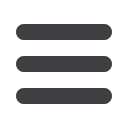
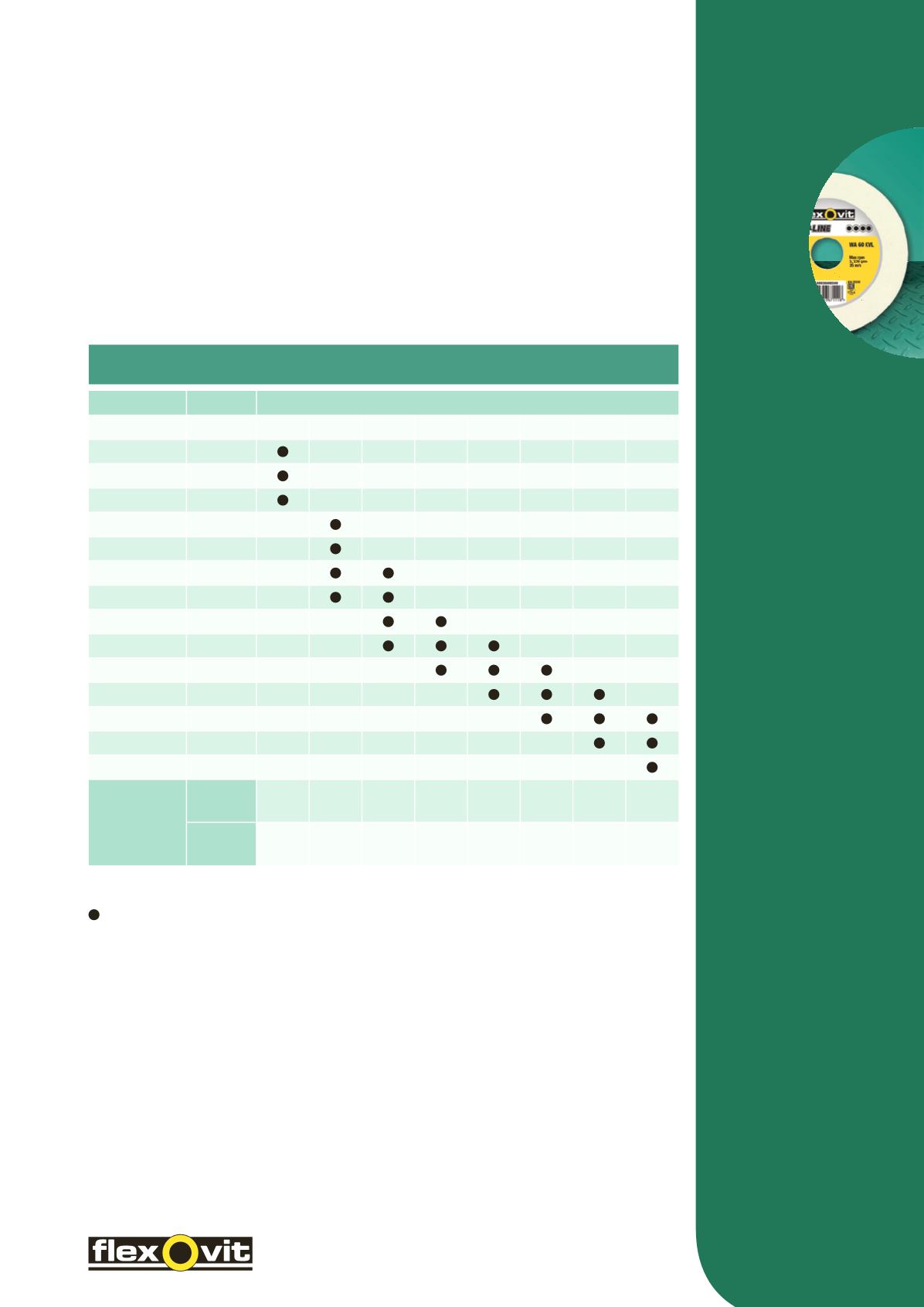
BONDED
ABRASIVES
233
SURFACE FINISH AND GRIT SIZE
Surface
Finish
Grain Size
μ in CLA μ m Ra 46 60 80 100 120 150 180 220
42
1,10
32
0,80
26
0,70
21
0,50
16
0,40
14
0,35
11
0,25
8
0,20
7
0,17
6
0,14
5
0,12
4
0,10
3
0,08
2
0,05
Min Form
Radius
Metric
mm
0,75 0,50 0,40 0,25 0,20 0,18 0,13 0,10
Imp
ins
.030 .020 .015 .010 .008 .007 .005 .004
Usage Key
strongly recommended
Achieving Improved Surface Finishes
By changing the wheel dressing technique, it is possible to achieve finer surface finishes than those shown
in the preceding table. As well as reducing the dresser infeed per revolution of the grinding wheel, it is also
possible to reduce the infeed and traverse rate when grinding, thus reducing the stock removal rate. Obviously
this approach will have limited application in production grinding but it can be very useful in toolroom work.
SURFACE FINISH
The achievable surface finish in any grinding operation is highly dependant upon the grit size of the grinding
wheel. The following chart shows the range of surface finishes achievable when using grinding wheels of different
grit sizes on conventional precision grinding applications, together with the minimum form radius that can be
ground using each grit size.
Other factors can affect the surface finish achieved. In particular:
• Production grinding applications, with higher stock removal ranges, will give surface finishes at the coarser end
of the range
• Plunge grinding applications will often require the selection of a grit size one size finer than shown
• Dressing techniques and the type of material can also affect the surface finish achieved