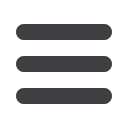
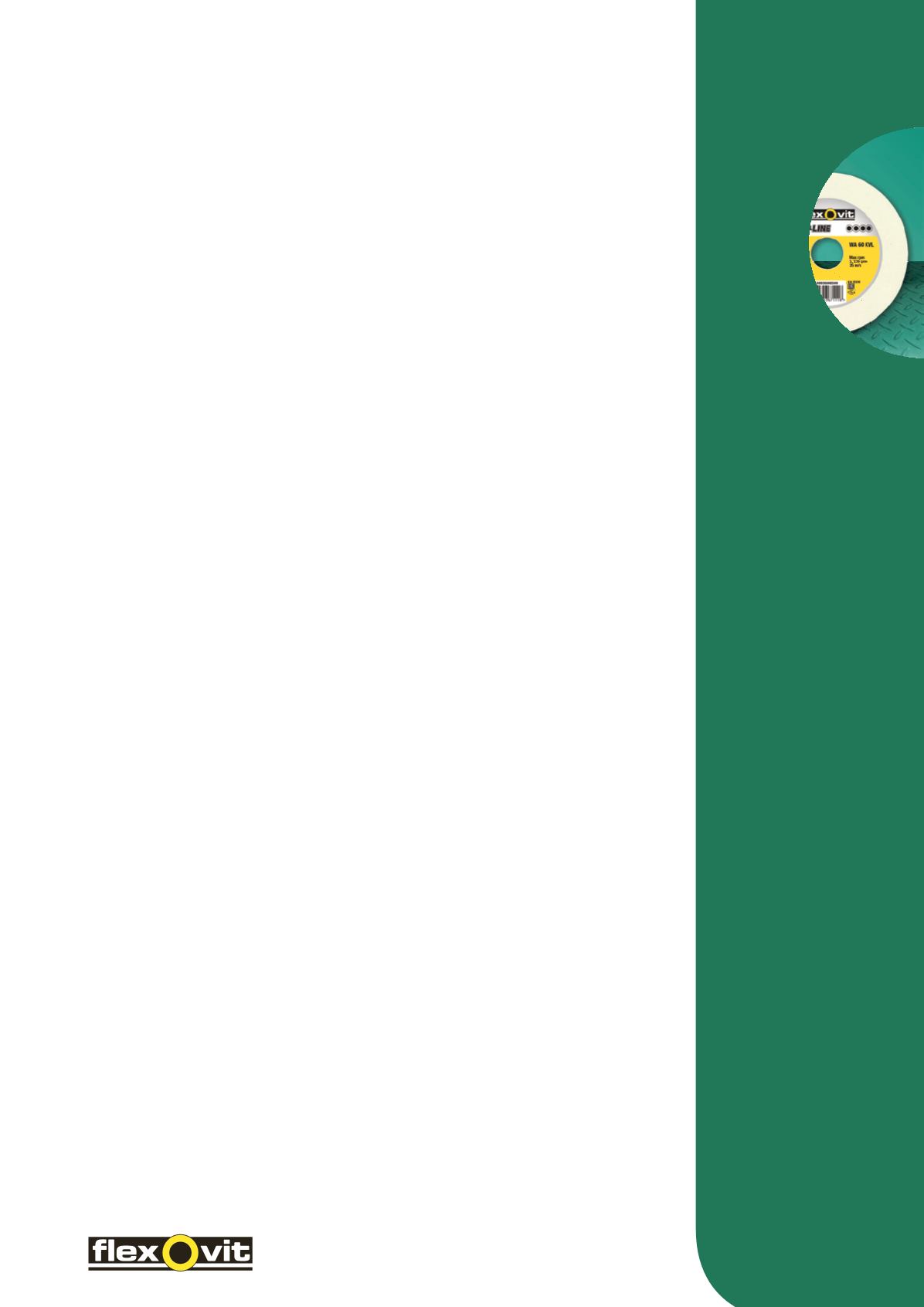
BONDED
ABRASIVES
235
MOUNTING
A wheel should only be mounted on to the machine for which it was intended. The speed of the spindle
on which the wheel is mounted should not under any circumstances exceed the maximum RPM speed specified
for the wheel when it is full size. The wheel should fit freely, but not loosely, on to the spindle or spigot diameter
of the flange plates. Wheels, blotting paper washers and flanges should be free from foreign matter. Certain
wheels have a positioning mark (Mount Down or Mount Up) marked on them. Care must be taken to ensure
that this mark occupies the position stated by the manufacturer.
REDUCING BUSHES
Where a removable bush is used as a means of reducing the bore of an abrasive wheel, care must be taken
to ensure the bushes should not project beyond the side of the wheel and the wheel blotter. The clamping
faces of the flange plates MUST clamp on the mounting washers attached to the wheel and not on any part
of the reducing bush. Reducing bushes should never be used on wheels less than 6mm thick or on products
with a back or web of less than 6mm. Never use plastic bushes in wheels used with portable grinding equipment.
MOUNTING WASHERS
Blotters should be used with all grinding wheels unless there is a specific exemption. Blotters should be slightly
larger in diameter than the mounting flanges and free from any scuffs, wrinkles or other damage.
MOUNTING FLANGES
Mounting flanges are designed to clamp the wheel to the machine and transfer the driving forces from the machine
spindle to the grinding wheel. They should be designed to take the driving forces away from the area around
the grinding wheel bore and generally should be not less than one third of the grinding wheel diameter.
Flange surfaces should be flat, free from burrs, bumps, bruises and other damage. Flanges should be of equal
diameter, have equal bearing surfaces and be properly recessed or undercut.
The rear flange must be positively driven by the machine spindle being either keyed or shrunk onto the spindle.
Flanges must run true to the machine spindle.
Clamping nuts (centre nut locking) should only be tightened sufficiently to hold the wheel securely without
slippage and must not be over-tightened. When flanges are clamped by a series of screws, they should be
tightened in stages uniformly in a diametric sequence.
In most instances it is appropriate to tighten the nut or screws by hand with the correct tool (spanner
or hexagonal socket key) until they stop turning. By adopting this technique it is very rare that the wheel would
be under-tightened and impossible to over-tighten the wheel. Bolts for mounting wheels with inserted nuts should
be long enough to engage an adequate length of thread, i.e. equal to the thread diameter, but must not protrude
through the nut insert.
For recommended designs of flanges, refer to the ‘FEPA’ Safety.
CAUTION
After mounting or re-mounting a grinding wheel on a machine, stand well clear, ensuring that there are no
persons in line with the wheel and allow the wheel to run free for two minutes. A remounted wheel should always
be treated as if it were a new wheel.
TYPE 06 CUP WHEELS – FIXED MACHINES
The diameter of the flange and paper washer inside the cup must be smaller than the diameter of the cup recess
to avoid any risk of radial pressure on the wheel. When used for work heavier than light tool and cutter grinding,
the back flange may be larger than that inside the cup but the recess diameter of both flanges must be equal.
MOUNTED POINTS & WHEELS
The spindle dimensions of the mounted point must be suitable for the collet being used and the spindle overhang
corresponding to the machine speed should be observed.
TYPE 31 GRINDING SEGMENTS
Segments are held by special chucks with suitable provision for adjustment to compensate for segment wear.
To prevent breakages segments should not protrude more than 1,5 times their thickness from the clamping chuck
face, and should be mounted with markings uppermost.