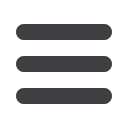
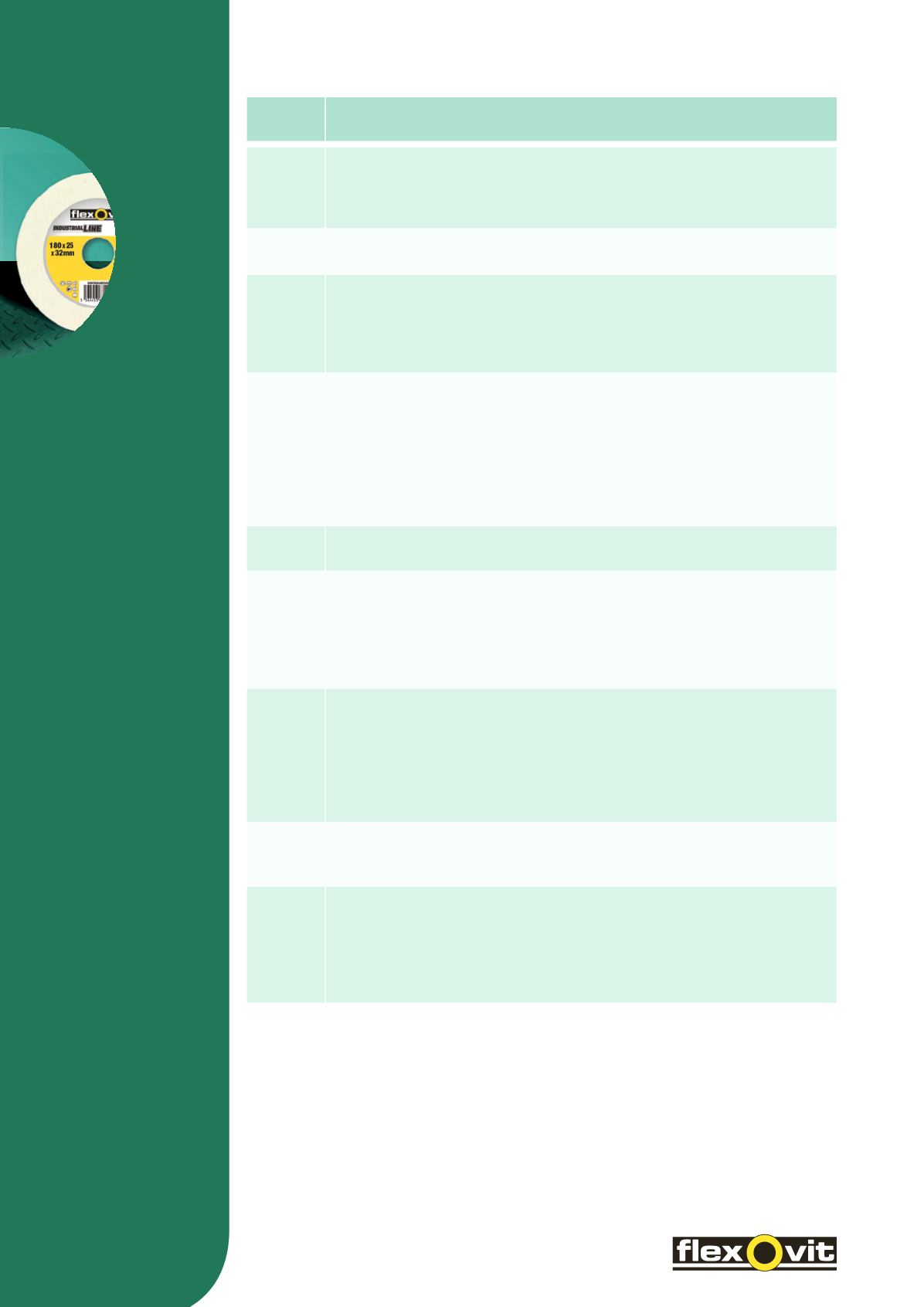
BONDED
ABRASIVES
236
Abrasive
Type
Description
41A
Pink Aluminium oxide is a highly refined form of alumina containing a small proportion
of chromium oxide. This addition makes 41A a little tougher than pure white, increasing
the strength along the shear planes.
This abrasive is available in a range of mounted points and wheels.
44A
Semi-pure brown fused aluminium oxide.
General purpose abrasive used in the range of resinoid cut off wheels.
48A
Semi-friable alumina, purity falls part way between conventional regular brown alumina
and white alumina. The resulting combination of friability and toughness gives wheels using
semi-friable alumina their free cutting characteristics.
This, combined with good form holding and a high degree of versatility, makes semi-friable
alumina is widely used for cylindrical, centreless, crankshaft and angle head grinding operations.
73A
A ceramic form of aluminium oxide that is harder and sharp than conventional abrasive grains.
This ceramic grain has a unique microcrystalline structure.
The structure of the grain allows individual particles to break away as they become dull.
This produces a very free grinding action that at the same time increases the number of parts
ground between dressings by up to 70%.
A high concentration blended with premium abrasives.
Used for grinding hard abrasive resistant steels and operations where high stock removal rates
are required.
79A
Blends of premium abrasives that include a low concentration of ceramic abrasive. Used in
toolrooms on high vanadium type steels.
A
This is a particularly tough form of aluminium oxide. Its toughness is due to the presence
of 3% of titanium oxide in the abrasive. Fired at low temperature the abrasive retains its natural
brown colour. Fired at high temperature further oxidation of the titanium oxide takes place
which changes the normal brown colour to a grey-blue. Because of its toughness, regular brown
alumina is suitable for grinding high tensile strength materials, specifically off-hand grinding
(bench grinding wheels) and sharpening stones.
C, GC
Silicon carbide abrasives are harder than the alumina type abrasives and are also more brittle.
Silicon carbide abrasive is used for grinding low tensile grey iron, chilled iron, cast iron, soft
bronze, copper, aluminium, stone, marble, rubber, hard facing alloys, and cemented carbides.
There are two varieties of silicon carbide, very similar in physical properties and mainly
distinguished by the colour. Black silicon carbide, is generally used for roughing operations
in coarse grit and resinoid wheels. Light green silicon carbide, is preferred for specific
applications such as most precision and carbide tool grinding.
52A
A blend of white and brown alumina, wheels containing this abrasive combine the toughness
of brown with the cool, sharper cutting of white alumina.
Used for sharpening engraving cutters and grinding hard chrome.
WA
White alumina is a highly refined form of aluminium oxide containing over 99% pure alumina.
The grain structure is made up of several crystals that allow the grain to breakdown along
the shear planes between the crystals as the grinding pressure increases. This gives wheels
containing white alumina a property called ‘friability’ (the ability to fracture, exposing sharp
cutting edges, as opposed to blunting). Used mainly for the grinding of very hard
or heat sensitive materials.
TECHNICAL INFORMATION